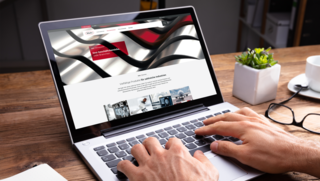













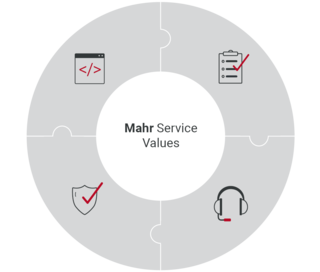






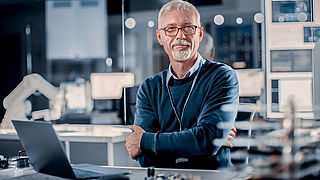
作为一家活跃于国际范围的公司,Mahr 不仅在德国拥有专利,在世界范围内也拥有专利。
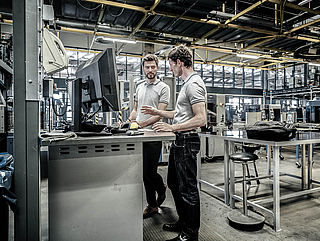






Mahr马尔 的创新手持测量设备:卡尺、千分尺和指针式指示表 – 包括模拟和数字型号及内置无线传输。Mahr马尔 的比较测量仪器和参考标准对于您的精密生产计量来说必不可少。
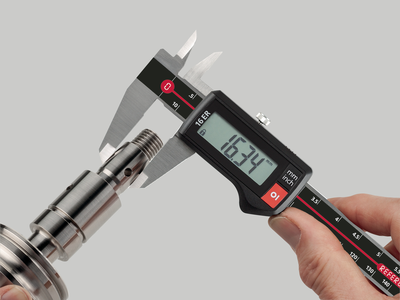
从模拟到数字的全系列卡尺。操作简单,无线,高准确度。在生产中高效率使用的完美选择。

安全、易读的数字显示屏、现代的设计以及常规精度是 Mahr马尔 数显卡尺的主要特点。范围包括测量仪器的所有应用。数据传输的各种接口和高达 IP 67 的保护等级可满足所有要求。

无眩光读数,硬化钢,凸起导轨,都可保护刻度和提供最大的准确度。Mahr马尔 的高质量卡尺,配备经典的游标。

可始终保持精度的大型高对比度度盘和防震测量工具。成熟的机械设计,可快速、安全读数。
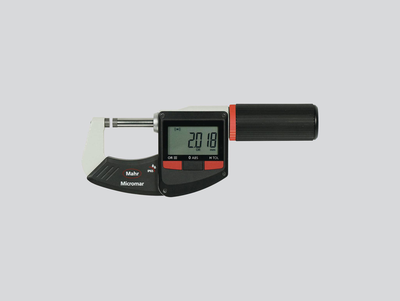
多种设计的最大精度。Mahr马尔 的千分尺提供传统的机械和数显以及无线版本。

清晰的数字显示屏、现代的设计以及常规精度是 Mahr马尔 数字外径千分尺的主要特点。范围包括测量仪器的所有应用。数据传输的各种接口和高达 IP 65 的保护等级可满足所有要求。

防眩光读数,隔热板和精密研磨主轴,最大限度地提高准确度。Mahr马尔 优质游标卡尺的特点。

特别适合批量零件(轴、螺栓、柄)的可靠、快速测试。尺寸精度在机械式比较仪上一眼就能识别和读取。

适合测量大直径和最大 2,500 mm 的测试距离

提供刻度或数字显示,或作为手枪握柄式快速测量仪器。Mahr马尔 三点内径测量设备拥有自动调心功能,可始终提供可靠的测量结果。
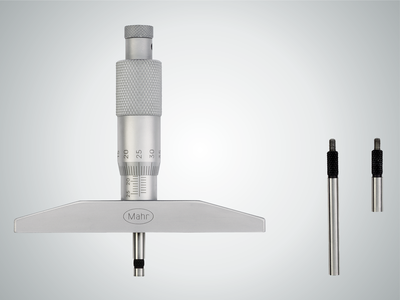
防眩光读数和精密研磨主轴,最大限度地提高了准确度。Mahr马尔 优质游标卡尺的特点。

从模拟到数字的机械式量规、机械式比较仪和机械式杠杆表的全系列。操作简单,无线(可选),高精度。在生产中高效率使用的完美选择。
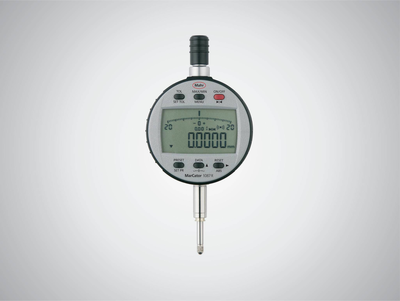
清晰的数字显示屏、稳固的结构和高精度是 Mahr马尔 数字机械式量规的主要特点。范围包括测量仪器的所有应用。数据传输的各种接口和高达 IP 54 的保护等级可满足所有要求。

高灵敏度和精度:测量工具轴、精密齿轮和小齿轮、高精度固定测量头的稳固安装。
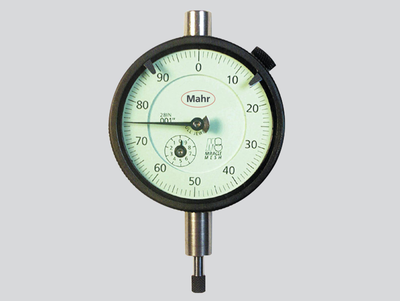
高灵敏度和精度:测量工具轴、精密齿轮和小齿轮、高精度固定测量头的稳固安装

与模拟机械千分表相比,Millimess 机械式比较仪有着更精确的元件,可提供更好的测量精度和更小的滞后误差。这些优点在跳动试验、直线度和平整度测量和比较测量中尤其明显。

高精度感应 Millimess 机械式比较器的数字增量高达 0.2μm。用户友好的操作功能,如公差监控、动态测量值的最小值或最大值记录、数字和分度的组合显示以及简单的数据传输,使其成为不可或缺的精密测量仪器。
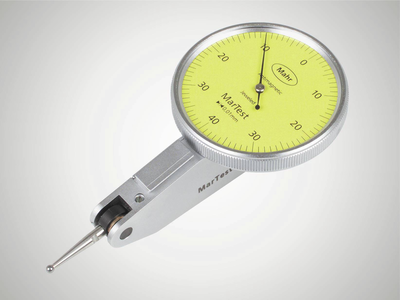
高灵敏度和计算机优化的测量工具确保了极高的安全性和精度。为了在环境恶劣的车间内使用,显示器采用硬化的矿物玻璃板,可有效防止划伤或破裂,同时采用了能够可靠地防止液体渗入的密封。
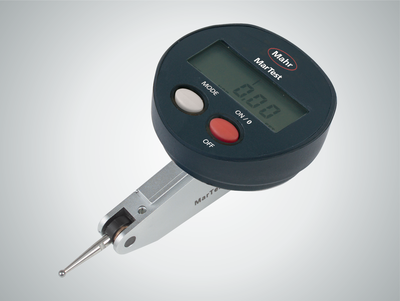
轻松易读的数字显示屏、稳固的设计和高精度是 Mahr马尔 数字机械式杠杆表的主要特点。
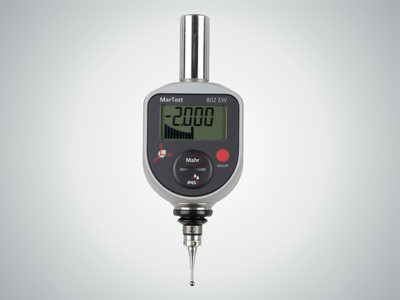
用于 NC 机器、加工中心和蚀刻机的 Mahr马尔 3D 测针可缩短设置与停机时间。非常适合精确接触工件和夹具上的参考边。

无论内置无线、外部无线模块、USB、Opto R S232 或 Digimatic 等:无论您使用何种接口标准,MarConnect 都能为您实现最佳的连接。

很多 Mahr马尔 精密量规都有数据输出及 MarConnect 接口。无论您使用 USB、Opto R S232 或 Digimatic 等何种接口标准,MarConnect 都能为您实现最佳的连接。

Mahr马尔 的无线传输范围可确保您在移动的同时获得高精度测量结果。现代、易用的测量方式 - 不受有线技术的限制。

MarStand 测量座、测量台和径向跳动量规提供了较高的稳定性,是精确测量结果的基础。它们为您的机械千分表、机械式比较仪、机械式杠杆表测量设备和测针提供了必要的支持。
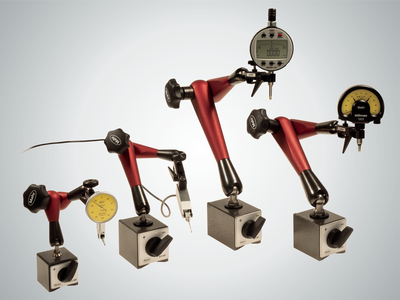
测量座设计稳固,是精确测量结果的基础。它们为您的机械千分表、机械式比较仪、机械式杠杆表测量设备和测针提供了必要的支持。
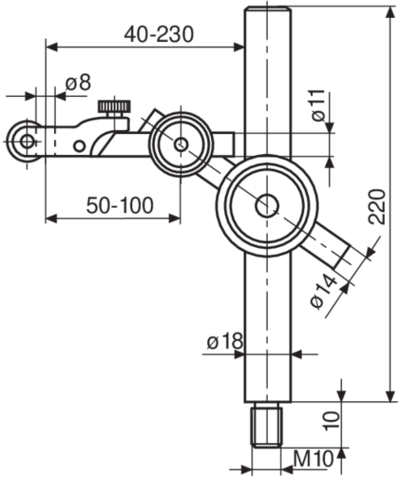
MarStand 支柱和支撑组件可用于单独的解决方案,提供了较高的稳定性,是精确测量结果的基础。它们为机械千分表、机械式比较仪、机械式杠杆表测量设备和测针提供了必要的支持。

测量台由精密水平测量台、稳定的测量柱和坚固的支撑臂部件组成。MarStand 测量台的稳固设计提供了较高的稳定性,是精确测量结果的基础。

径向跳动量规是在接近生产环境下检测轴位置和形状误差的最简单方法。因其型号多样,坚固耐用的 MarStand 径向跳动测量仪是满足多种工件要求和提供精确测量结果的基本设备。
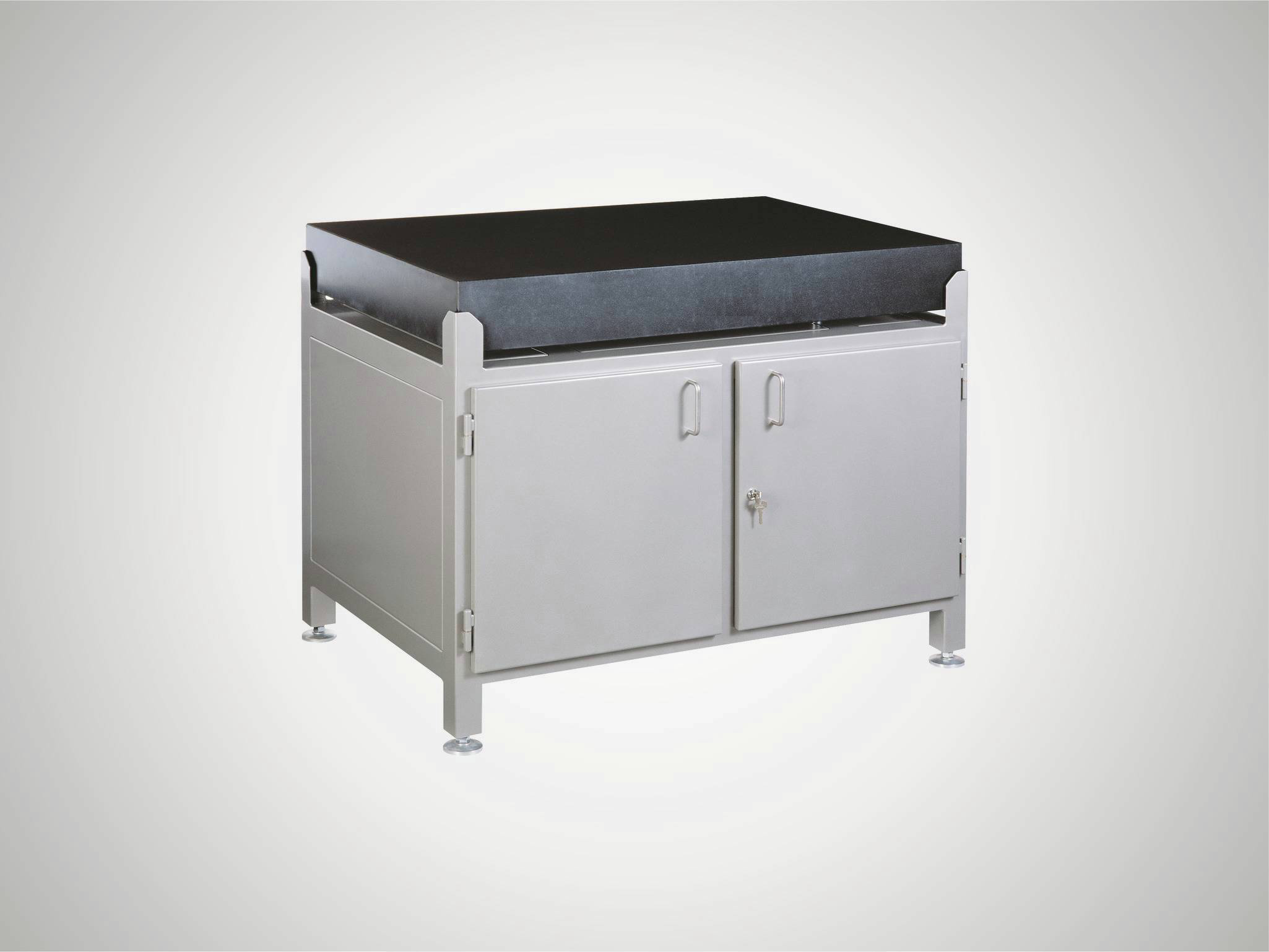
由硬质花岗岩制成的测试板具有较高的强度和尺寸稳定性,是测高仪器的完美表面。

将指示量规作为比较量规使用,成为生产中精密测量的理想工具。按参考标准标定量规可降低偏差和最大限度地减少温度波动对测量结果的影响。

精密指针式卡规是精密测量轴、螺栓、柄等圆柱形零件的理想工具,特别适用于系列零件的安全快速测量。尺寸精度在机械式比较仪上一眼就能识别和读取。
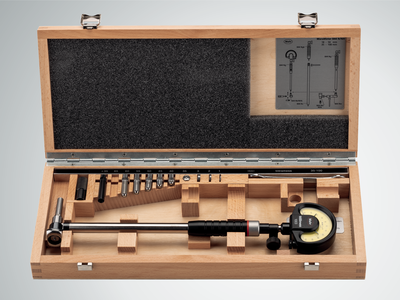
内径测量设备是测量孔的直径、圆度和圆锥度的完美工具。

厚度量规提供的测量范围广泛、简单,特别适合快速测量各种薄膜,板材和板。

如果由于工件的几何形状而不能使用卡尺或内径千分尺等常用测量仪器,卡尺是完美的解决方案!

深度量规提供的测量范围广泛、简单,特别适合快速的深度测量。8 mm 固定轴可根据测量任务使用检查机械千分表、机械式比较仪或测针。

通用测量仪器是生产中精密测量的理想工具,可将测量结果与参考标准进行比较,从而最大限度地减少温度波动对测量结果的影响。

无论齿轮、螺纹、圆锥度或凹陷度如何:Multimar 通用测量仪器是几乎所有不适合使用标准测量仪器的内外尺寸测量的理想解决方案。有多种基本装置和各种配件可供选择。
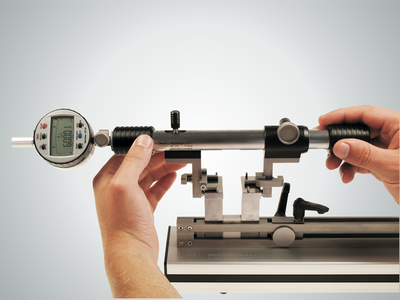
精确调整内外径测量仪器。使用 844 S 标定仪器时,您可以完美地完成每项测量任务,甚至可以用于更大的尺寸。

无论是调心肩,窄领还是凹陷:Multimar 36B 通用测量仪器是几乎所有内外尺寸测量的理想解决方案。有多种基本装置和各种配件可供选择。
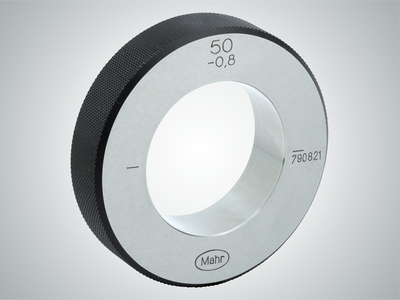
信任 Mahr马尔 的设置标准和量规 - 它们是精确测量结果的基础。
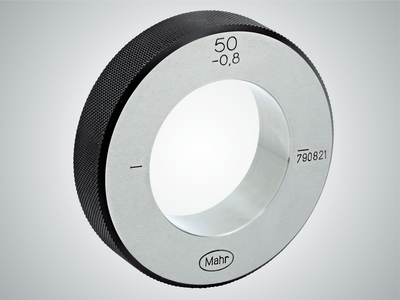
信任 Mahr马尔 的设置标准 - 它们是精确测量结果的基础。

Mahr马尔 量块确保了您可随时使用高质量的参考和工作标准。从四个公差等级和两种材料中选择以满足车间、生产或质量保证的要求。

Mahr马尔 针规有三个公差类别和各种设计。选择满足车间、生产或质量保证要求的设备。

人们对电子长度测量仪的要求几乎和其应用一样多样。要求高可靠性、高精度和简单操作。
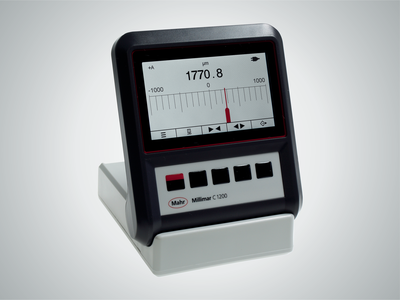
人们对电子长度测量仪的要求几乎和其应用一样多样。要求高可靠性、高精度和简单操作。Millimar 紧凑和立柱测量仪器满足了这些要求。
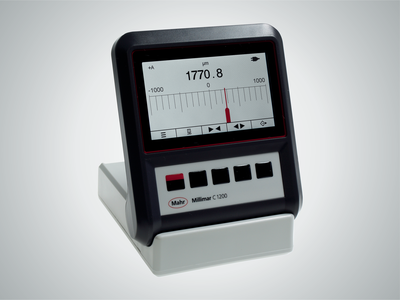
Millimar 长度测量仪紧凑、耐用和易用。它们是多功能的评估和指示工具,用于测量生产区域和测量室中复杂程度可控的任务。
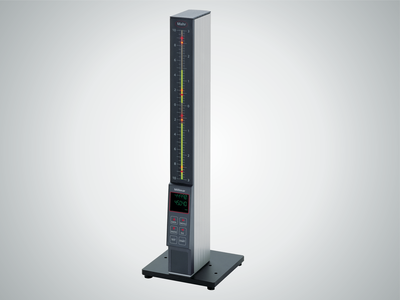
测量结果显示在 101 个三色 LED 上,可轻松从远处读取。如果超出可编程的警告和公差限制,则各部分会从绿色更改为黄色或红色。

模块和软件的多样化组合选项提供了比以往更高的设计工作环境和工具的自由度。

Smart and universally applicable software for complex measurement tasks in the manufacturing sector

Millimar 传感器是测量流程中最重要的元件之一。它们的特性决定了整个测量的质量。取决于应用,可为此组合使用多种技术。例如,Millimar 电感测头:这些产品坚固耐用,用途广泛,价格诱人。

无论是厚度测量、径向跳动或同心度:使用电感测头可记录测量值和偏差,而不受形状、支撑或径向跳动偏差的影响。其最大优点在于线性范围大,对干扰相对不敏感。测针主要用于生产中的比较测量,但传感器的具体任务可能会有所不同。

气动量仪具有精度高、长期稳定等特点。测量喷嘴的无接触测量不会损坏工件。即使是未清洗、涂油、润滑或涂有研磨膏的工件

Millimar 长度测量仪紧凑、耐用和易用。它们是多功能显示和评估设备,用于测量生产区域复杂程度可控的任务。

测量结果显示在 101 个三色 LED 上,可轻松从远处读取。如果超出可编程的警告和公差限制,则各部分会从绿色更改为黄色或红色。
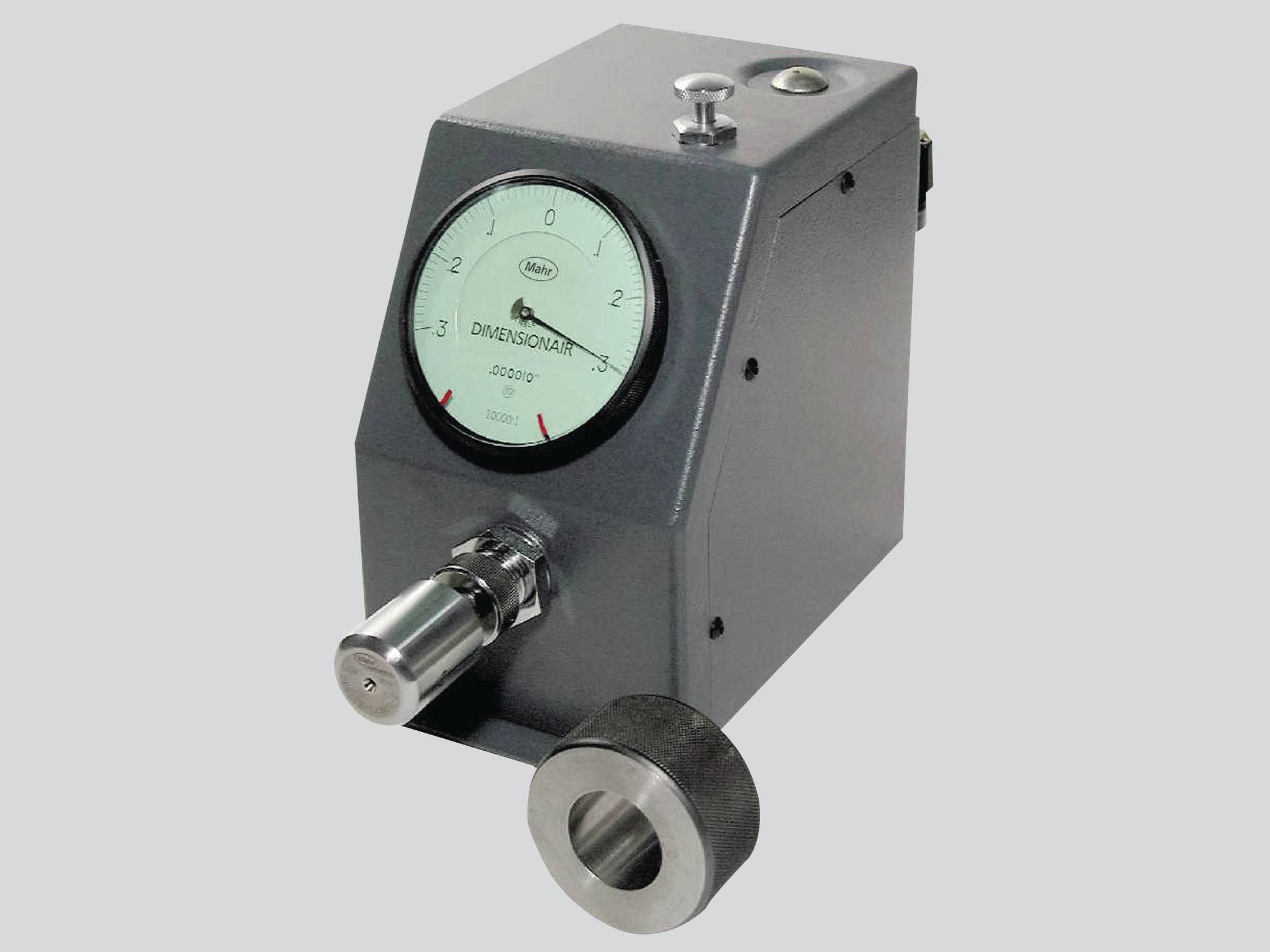
Millimar 气动测量设备可快速、准确地记录尺寸偏差。多年来也在工业生产和计量室中成熟应用。

用于测量和评定。

非接触测量,采用气动测量环,对工件无损伤。
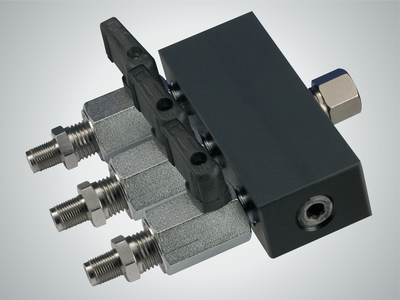
使用气动测量技术附件改造测量站以适应您的测量任务。
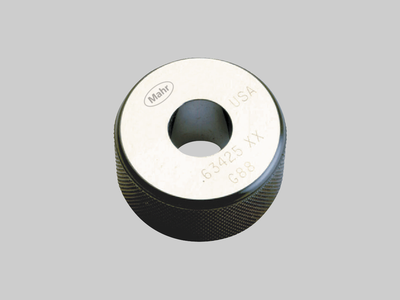
信任 Mahr马尔 的设置标准 - 它们是精确测量结果的基础
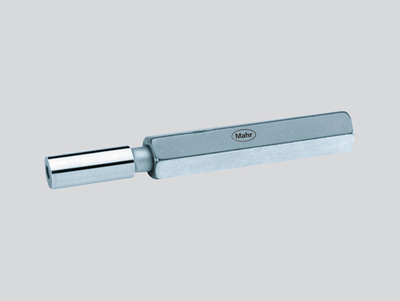
设置气动测量仪(气动环规)硬化、老化、打磨、抛光的精细工艺。
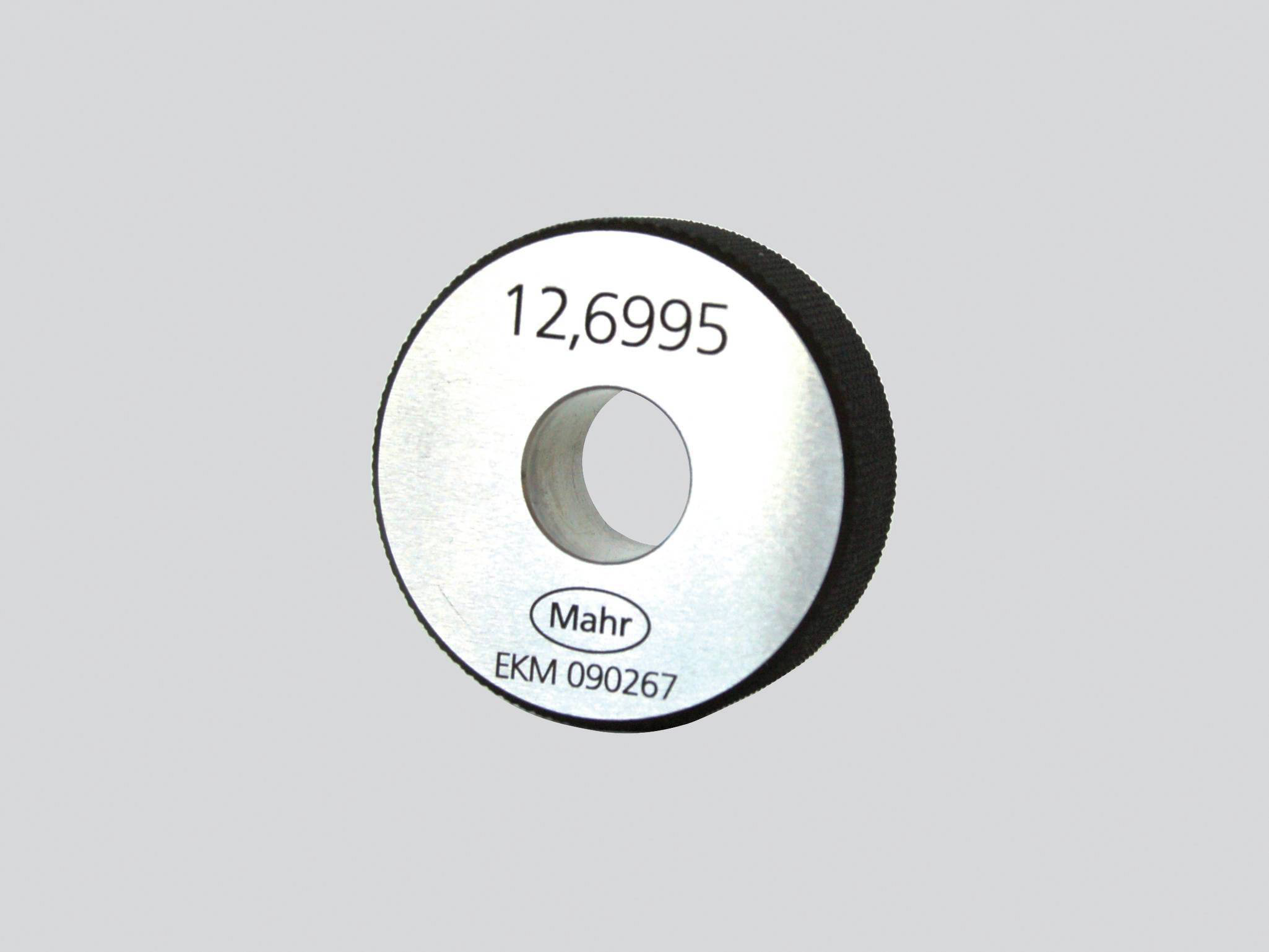
设置气动测量仪(气动环规)硬化、老化、打磨、抛光的精细工艺。
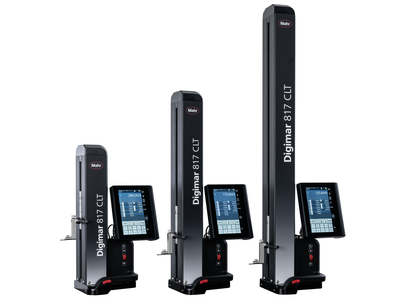
想要更好的测量结果?Digimar 是最适合的选择!

用于车间中工件的划线和标记。轻松测量高度及距离。
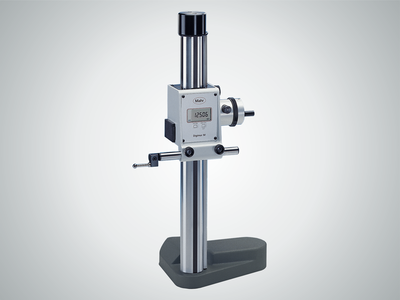
轻松测量孔、表面和边缘的高度以及之间的距离。适合划线和标记带额外附件的工件。
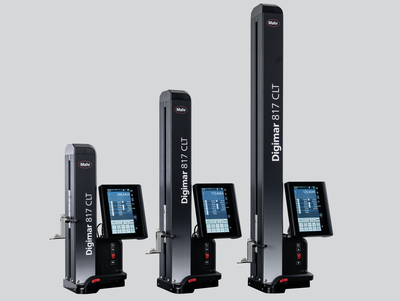
触摸式操作,符合人体工程学的处理方式和广泛的评估选项: 这就是Digimar 817 CLT高度测量仪所代表的意义。
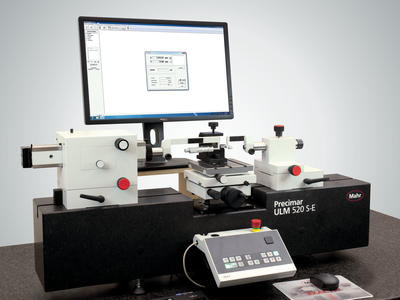
精密长度计量代表着绝对和相对测量中的高精度尺寸度量技术。
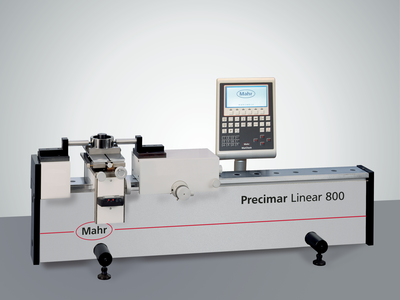
车间通用、易用的长度测量和设置设备
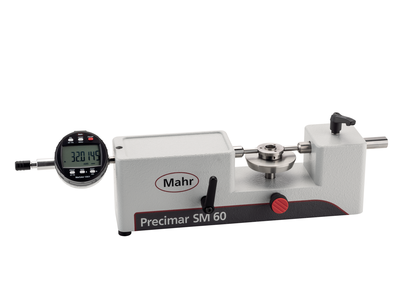
车间通用、易用的长度测量和设置设备
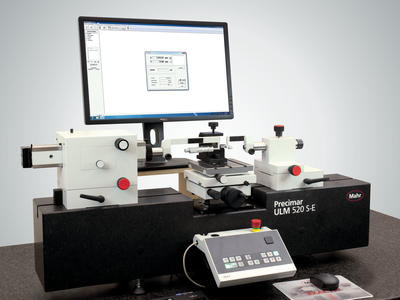
Mahr马尔 的产品系列从简单的量块测试架、全自动机械式量规测试架和 ULM 设备到超精确半自动化 CiM 通用测量机,为制造、测量室和校准实验室提供了实用的解决方案。换句话说:同时具备最大精度和极高效率的测量流程。

无论是经典的 ULM 或电动 PLM 和 CiM 仪器。Mahr马尔 通用长度测量仪支持用户友好、快速而可靠的测量,同时不确定性极低。

机械千分表、机械式杠杆表测量设备、机械式比较仪和测针的半自动和全自动测试 - 高效、精确。
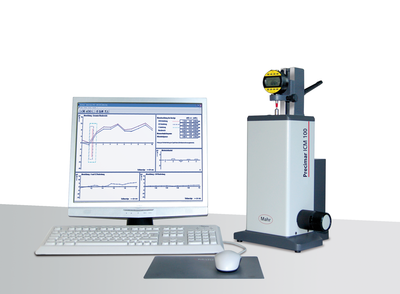
机械千分表、机械式杠杆表测量设备、机械式比较仪和测针的半自动和全自动测试 - 高效、精确。

使用指示表、杠杠表和比较仪的手动测试——轻松、精确
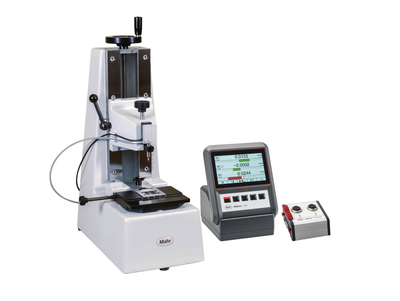
信任 Mahr马尔 的量块比较器 - 它们是精确检测您的标准的基础
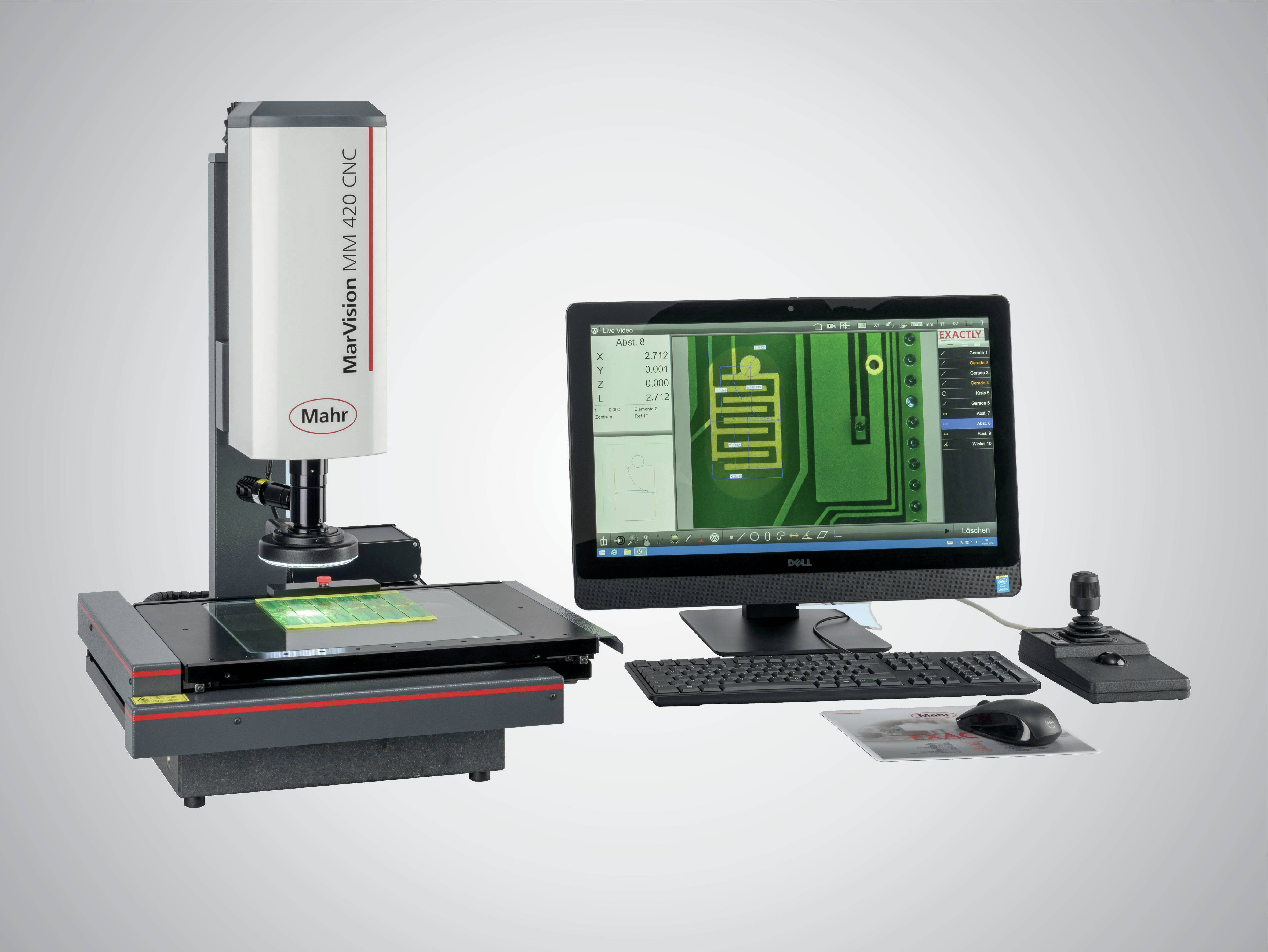
几乎所有行业都要使用显微镜进行快速的距离、半径和角度检测。实验室中或接近生产。
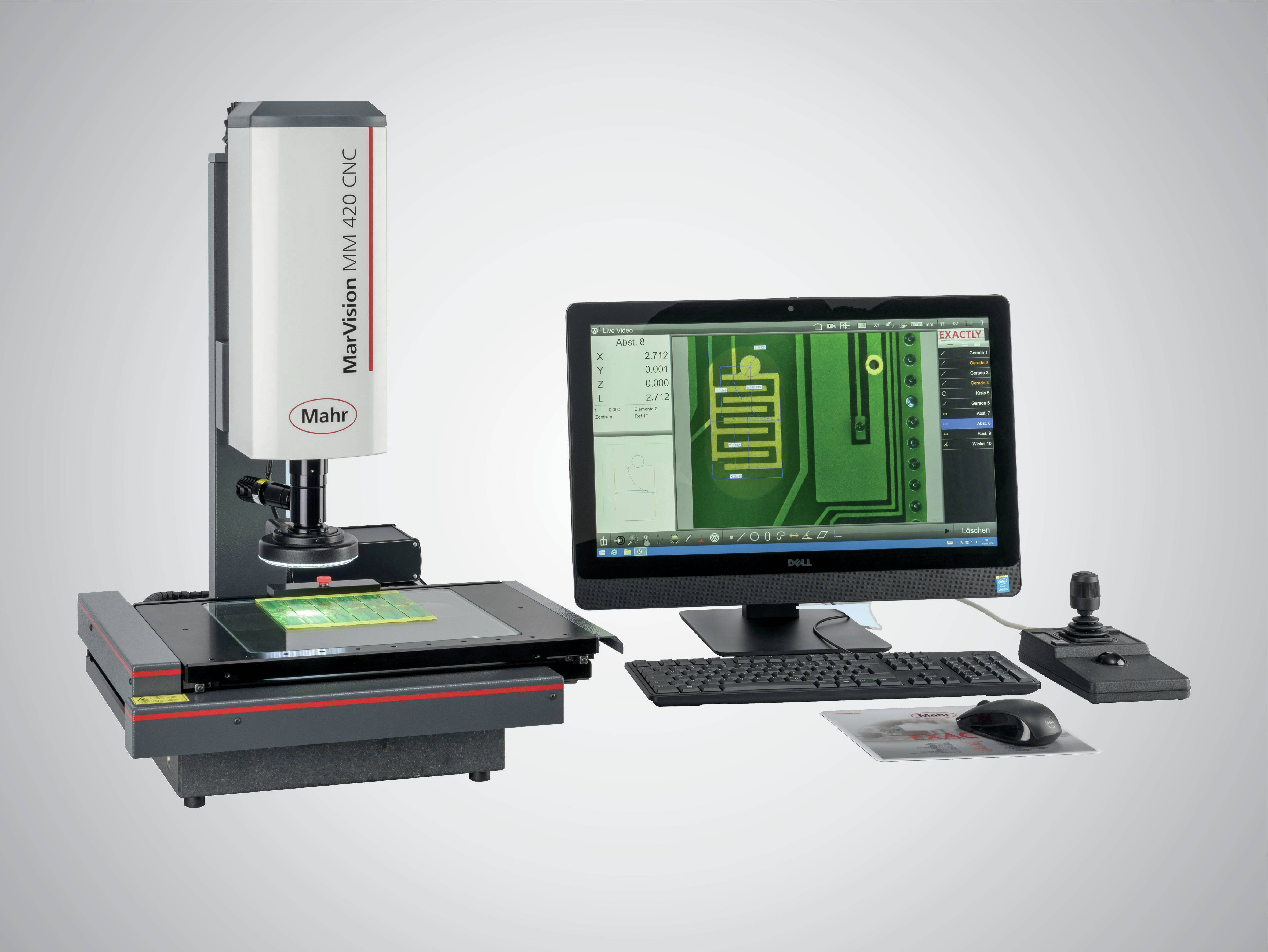
几乎所有行业都要使用显微镜进行快速的距离、半径和角度检测。实验室中或接近生产。
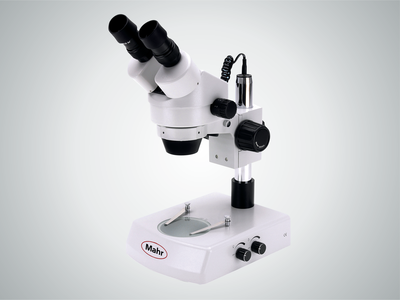
立体变焦显微镜与高质量镜头,用于明亮、锐利的三维图像。双目或三目,采用额外的数字相机。
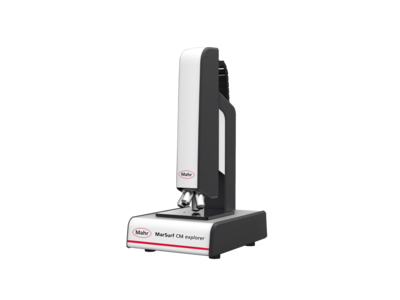
表面计量方法,工业和研究用
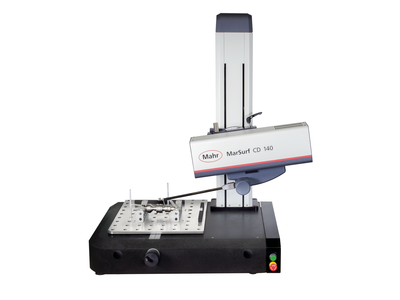
公差要求严格的结构功能表面要求可在较短时间内记录工件或物体表面特征轮廓的高精度测量系统。
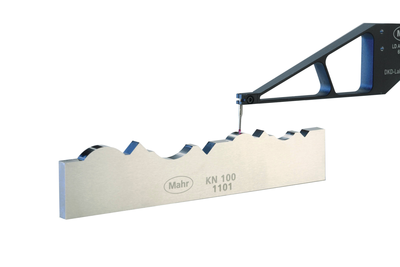
轮廓测量技术用于确定粗糙形状的偏差。
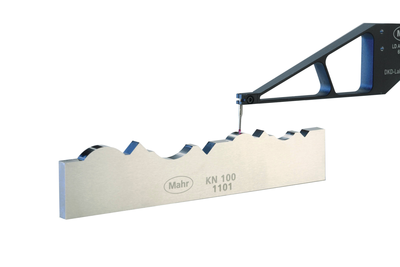

使用光学测量仪精密测量轮廓
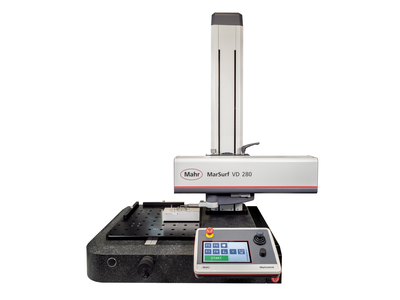
综合轮廓和粗糙度测量:专业型全能选手

综合轮廓和粗糙度测量:专业型全能选手
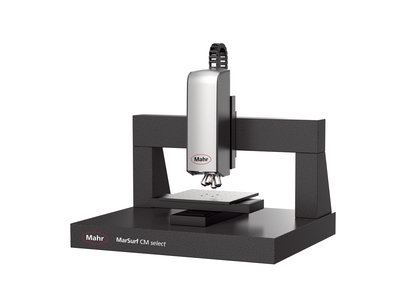
符合 ISO 25178 / ISO 4287 的 2D / 3D 轮廓及粗糙度测量
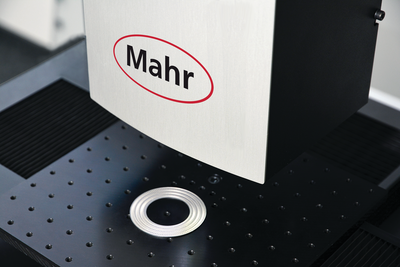
3D 表面度量方法,用于工业和研究
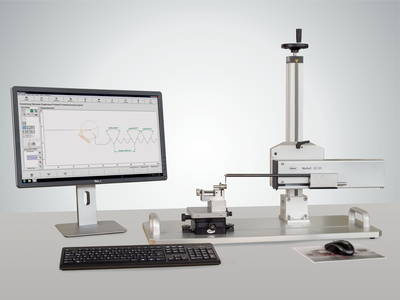
使用移动测量设备随处测量!

测量站,用于测量高精度镜头
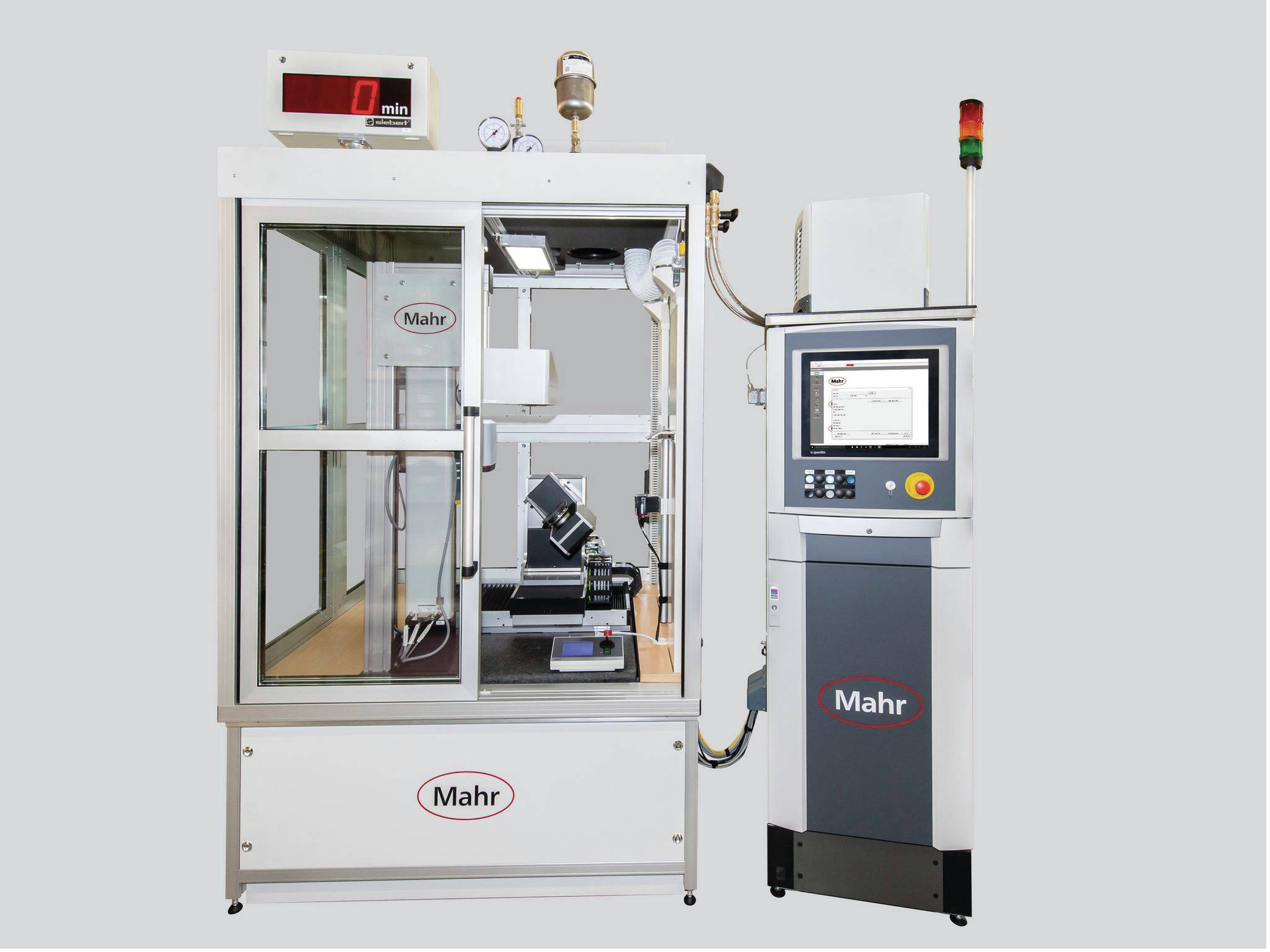
标准解决方案不再满足需求时:自定义解决方案
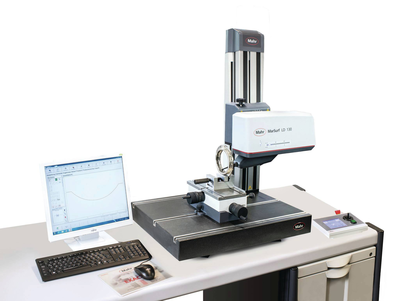
公差要求严格的结构功能表面要求可在较短时间内记录工件或物体表面特征轮廓的高精度测量系统。
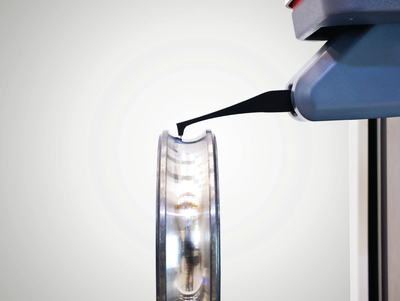
灵活而强大,可用于测量室和实验室
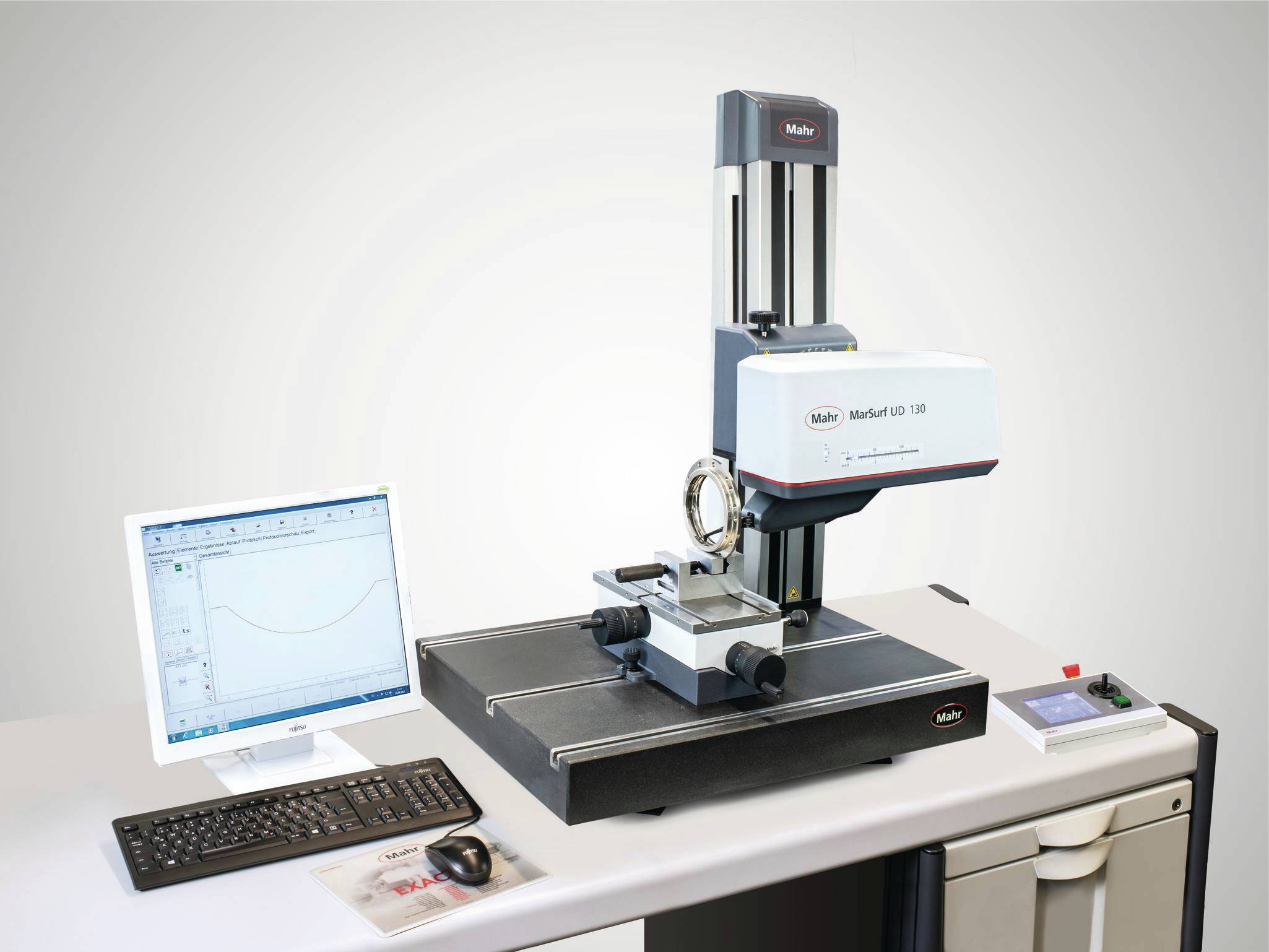
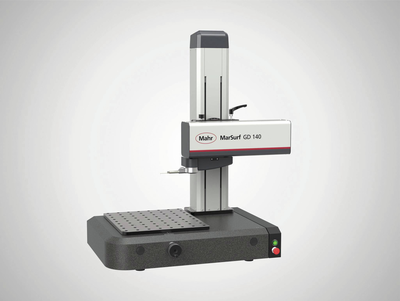
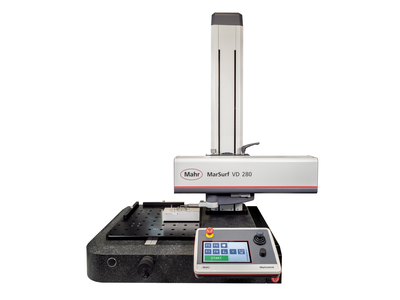
综合轮廓和粗糙度测量:专业型全能选手

触觉测量站,用于轮廓和粗糙度测量
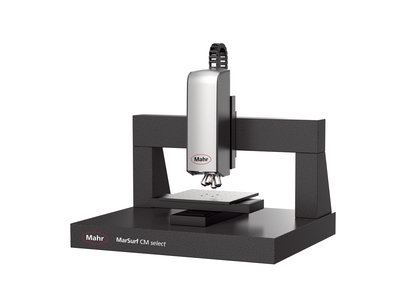
符合 ISO 25178 / ISO 4287 的 2D / 3D 轮廓及粗糙度测量
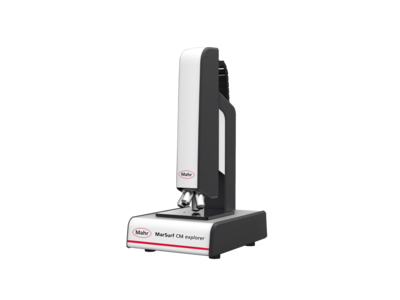
3D 表面度量方法,用于工业和研究

使用移动测量设备随处测量!
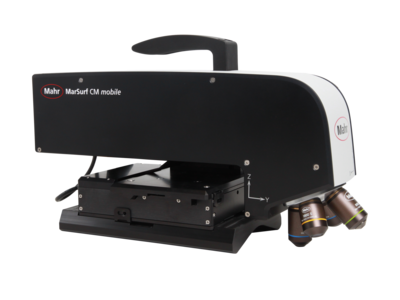
移动 3D 表面度量方法,用于
现场使用

移动测量仪器允许您在所需结果之处直接测量。

用于测量超高灵敏镜头的测量站
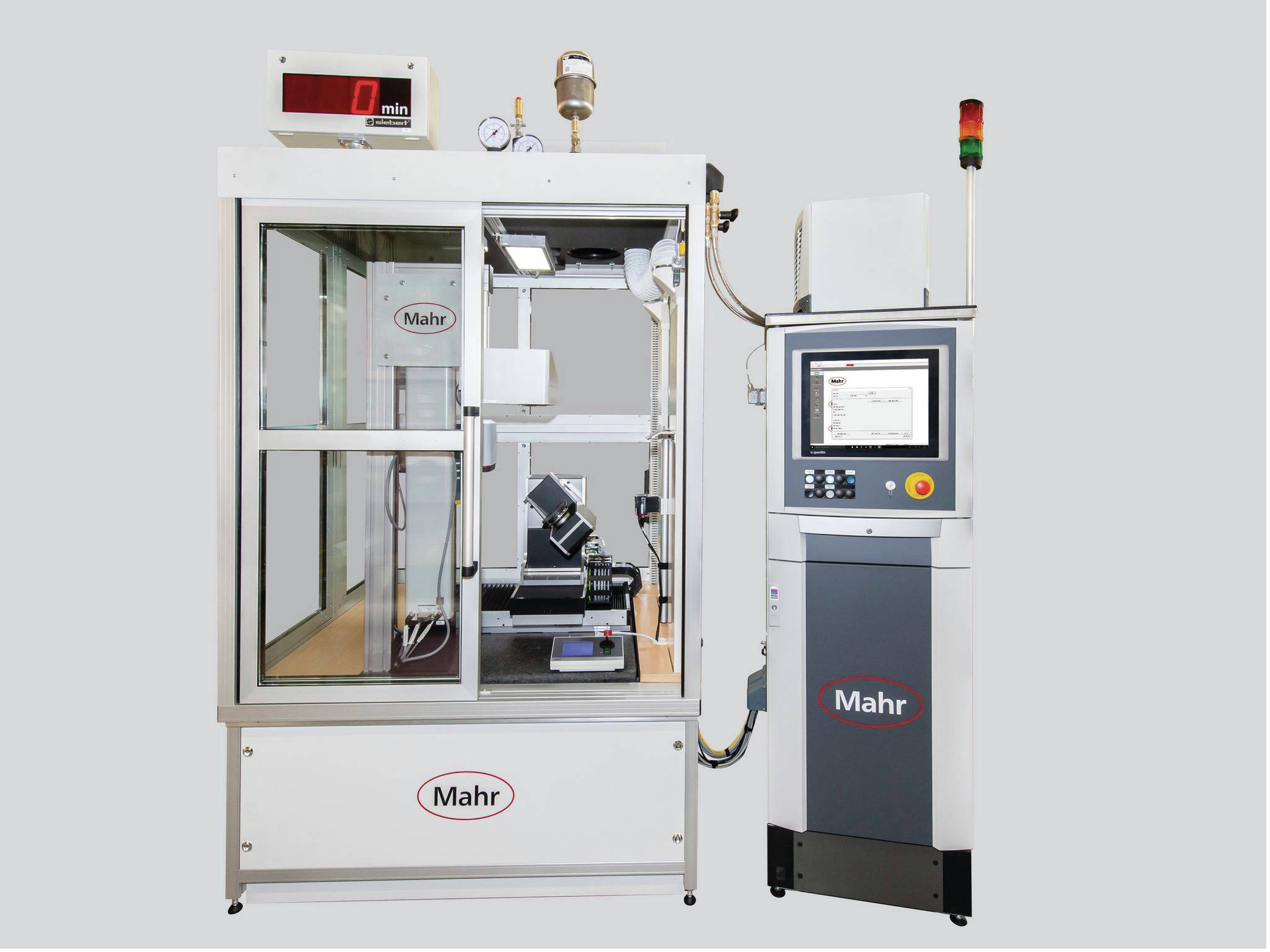
标准解决方案不再满足需求时:自定义解决方案

Metrology
Experience outstanding features combined with extreme flexibility in workpiece size and increase your productivity in the production environment.
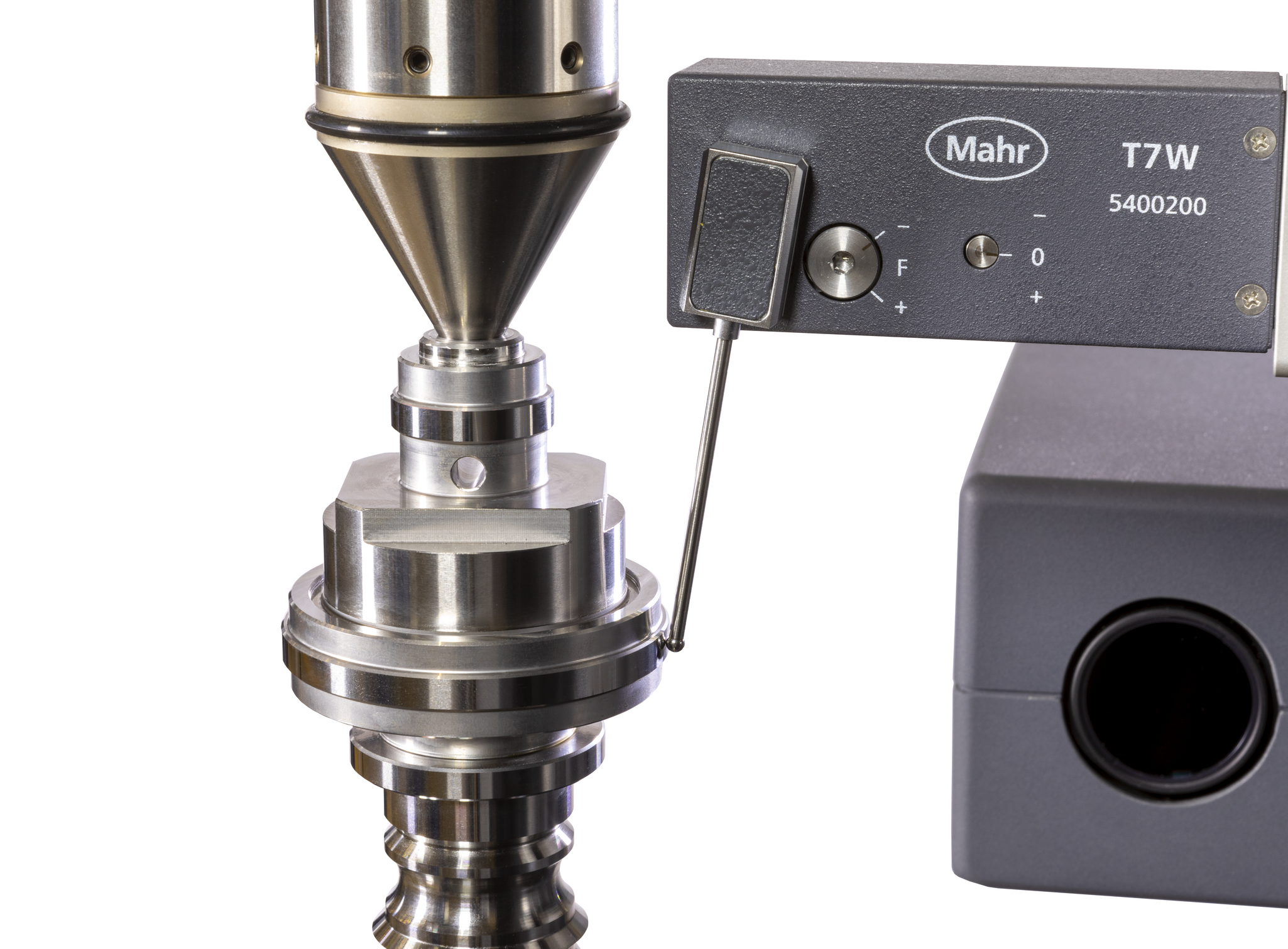
Fast optical matrix camera in combination with high-precision touch probes for measuring a large number of features on rotationally symmetrical workpieces.
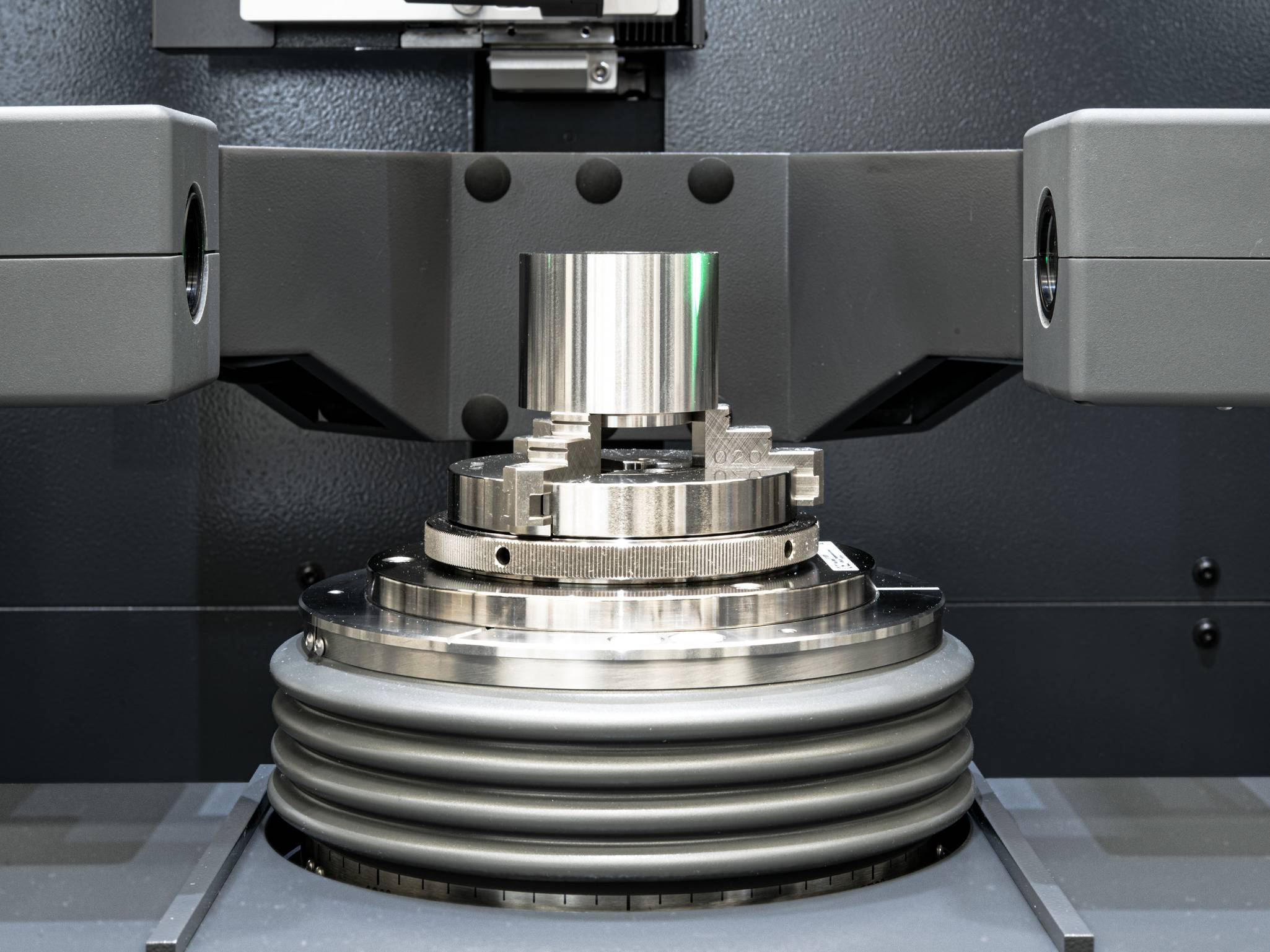
Fast optical matrix camera in combination with high-precision touch probes for measuring a large number of features on rotationally symmetrical workpieces. Addition of a fully automatic centering and tilting table for extremely fast, mechanical alignment, flexible clamping options and, for example, internal measurements.

测试形状和位置公差的系统,例如粗糙度、平面度、直线度、同轴度和其他测量任务。从手动到完全自动。
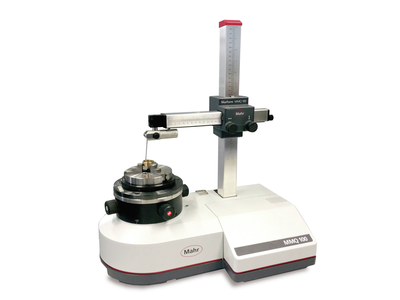
识别可简单、经济、高精度地测量圆度、直线度、同心度等。 我们的手动形状测量仪器适合测量室和接近生产区域的测量。
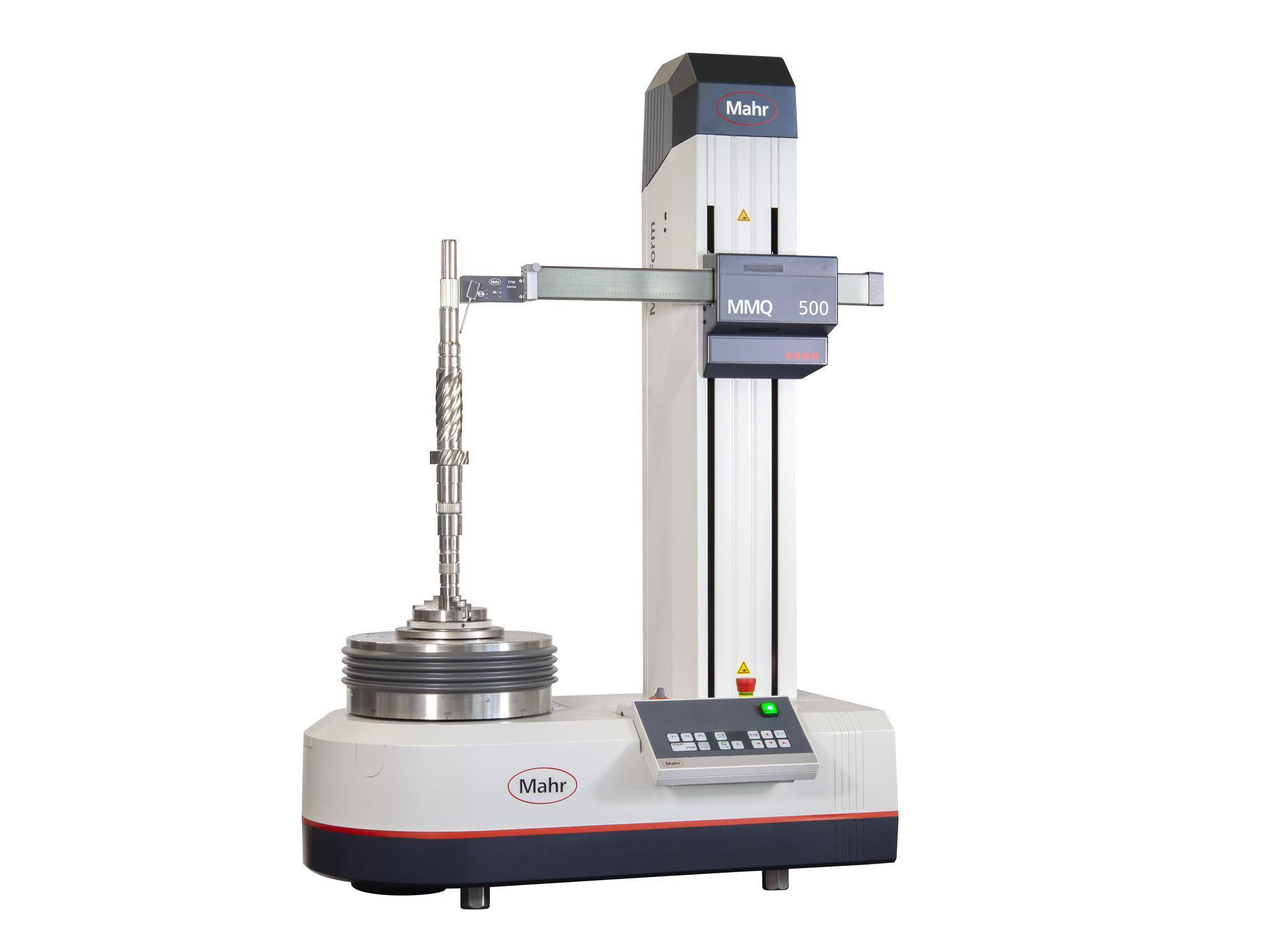
我们的自动形状测量系统支持您通过具备极高自动化、灵活性和准确性水平的稳定创新设备而降低工艺成本,同时不会增加检测成本。
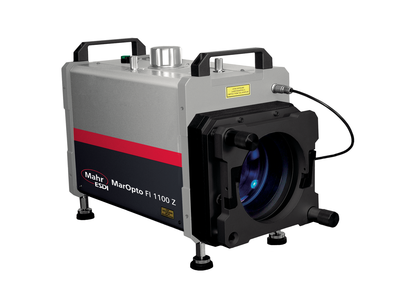
强大的 MarOpto Fizeau 干涉仪可以提供平面和球面的非接触测量。

Metrology
Experience outstanding features combined with extreme flexibility in workpiece size and increase your productivity in the production environment.
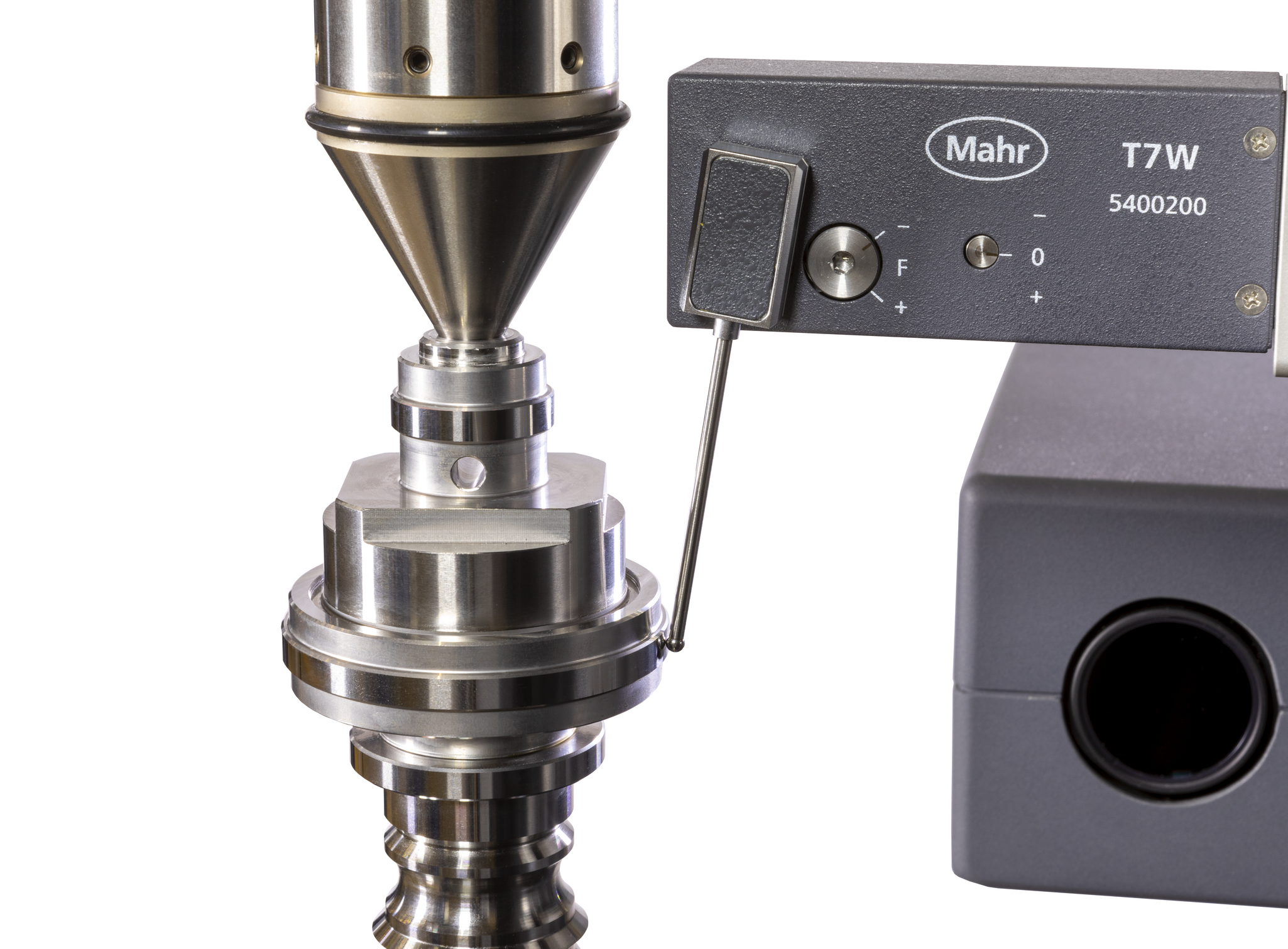
Fast optical matrix camera in combination with high-precision touch probes for measuring a large number of features on rotationally symmetrical workpieces.
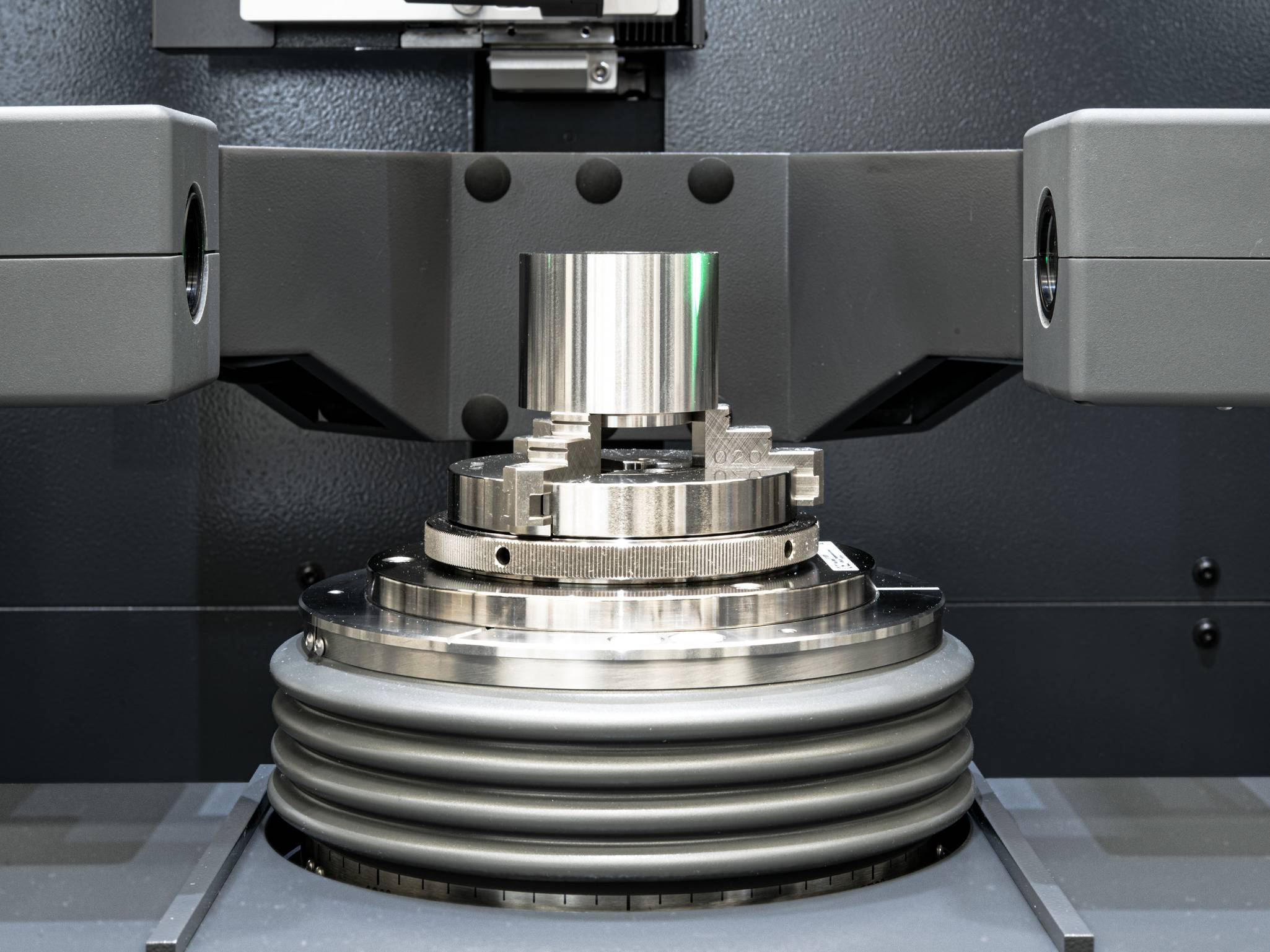
Fast optical matrix camera in combination with high-precision touch probes for measuring a large number of features on rotationally symmetrical workpieces. Addition of a fully automatic centering and tilting table for extremely fast, mechanical alignment, flexible clamping options and, for example, internal measurements.

光学和接触式轴测量系统,用于 严苛的生产环境中。 所有普通旋转对称工件的完整测量.
.
光学和触觉轴测量系统,用于 用途 in 严苛的生产环境中。 所有普通旋转对称工件的完整测量.

通用、全自动和牢固的光学轴测量机器,可适应恶劣的车间环境。

Metrology
Experience outstanding features combined with extreme flexibility in workpiece size and increase your productivity in the production environment.
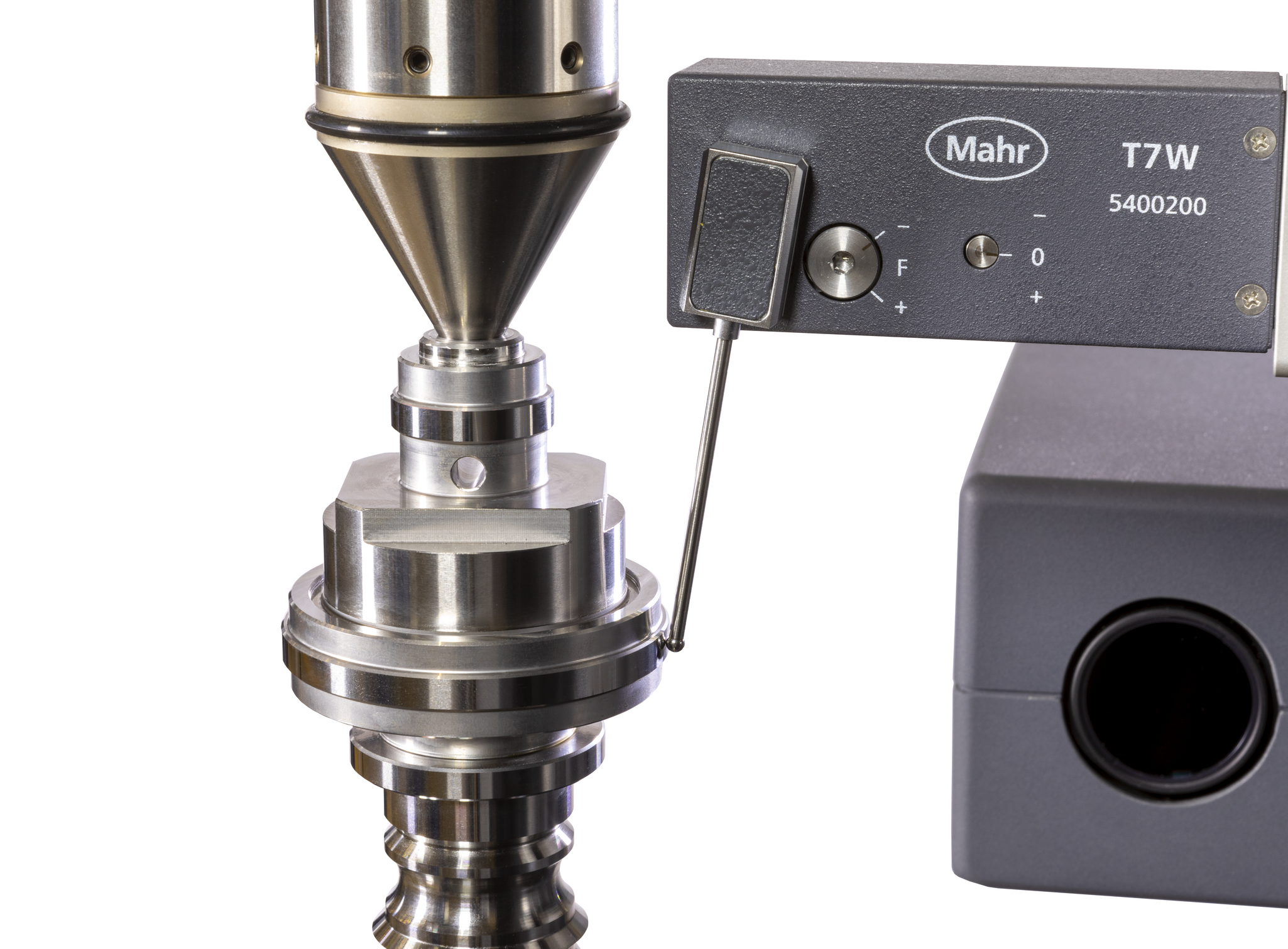
Fast optical matrix camera in combination with high-precision touch probes for measuring a large number of features on rotationally symmetrical workpieces.
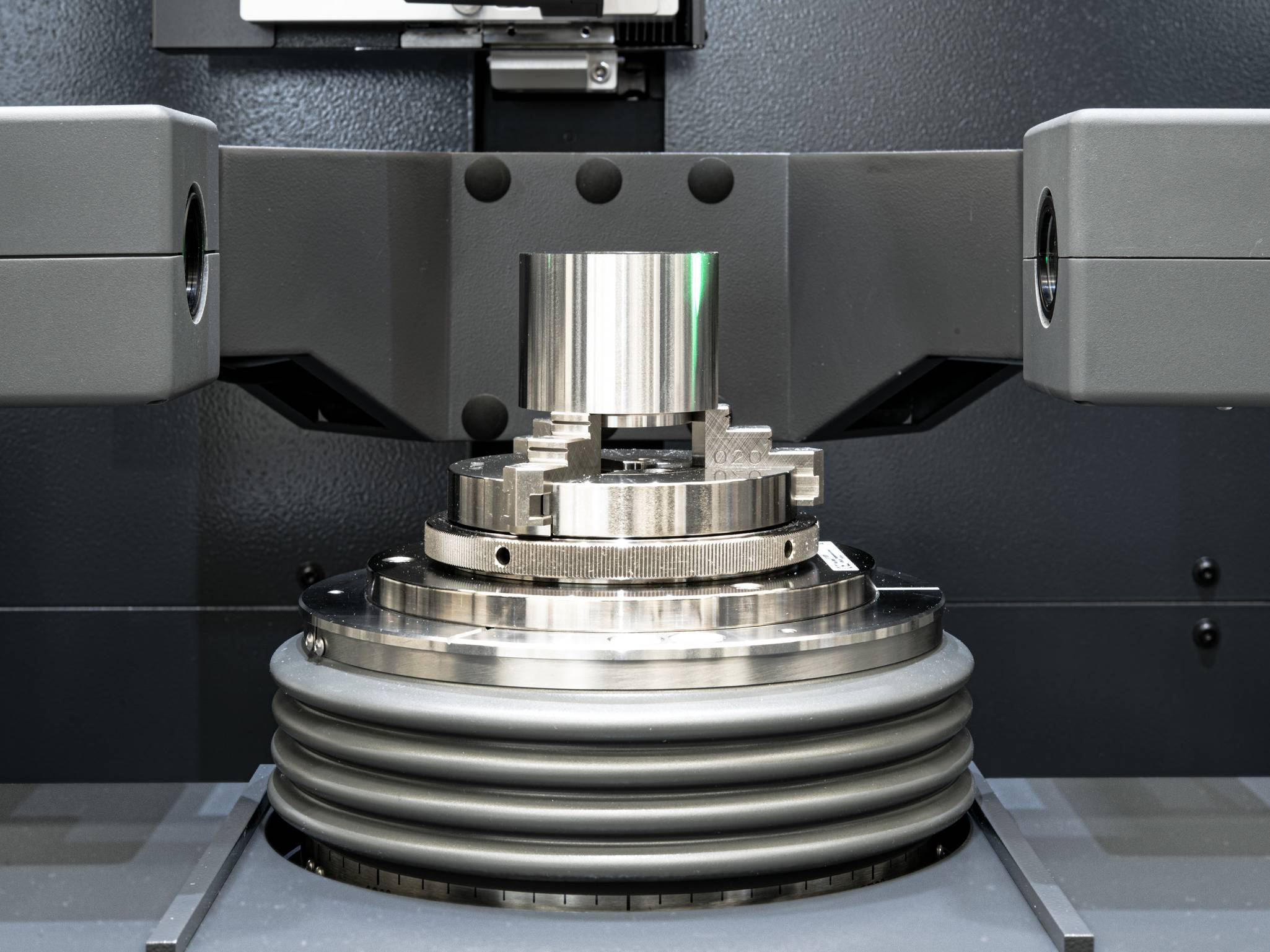
Fast optical matrix camera in combination with high-precision touch probes for measuring a large number of features on rotationally symmetrical workpieces. Addition of a fully automatic centering and tilting table for extremely fast, mechanical alignment, flexible clamping options and, for example, internal measurements.
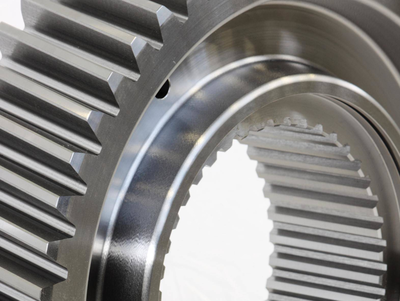
从高度专业的齿轮分析到完全集成的系列测量 - Mahr马尔 都是面向现代齿轮和变速箱生产各个层次的完美解决方案。

在产品最初阶段测量产品,包括快速反馈制造工艺以避免浪费。


多种技术和产品,可实现表面和几何形状的快速、无接触测量。
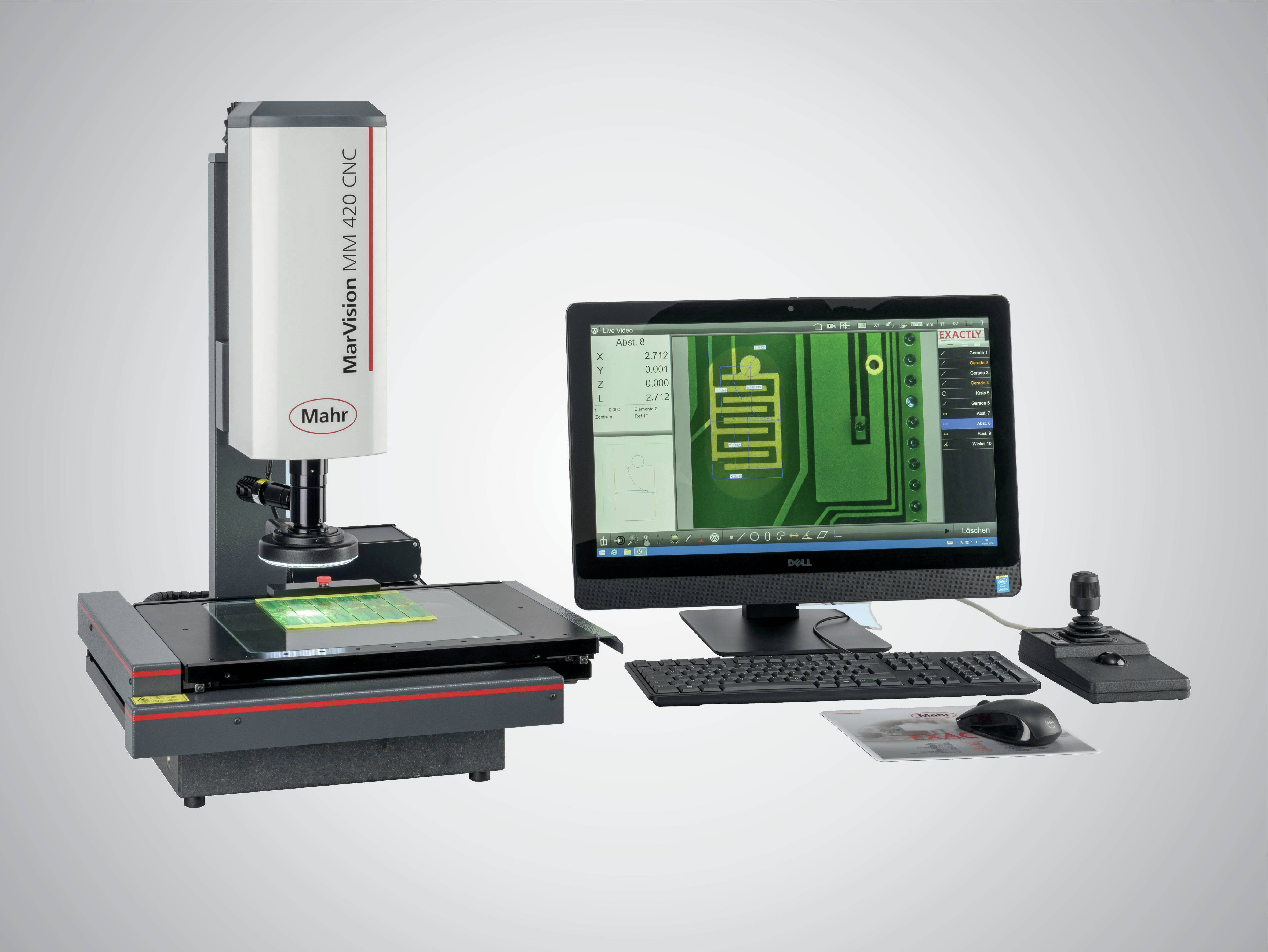
几乎所有行业都要使用显微镜进行快速的距离、半径和角度检测。实验室中或接近生产。
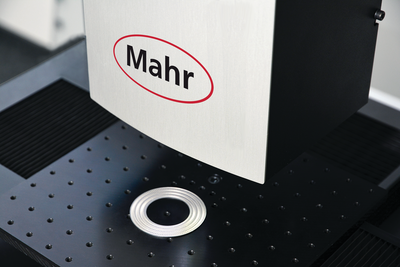
粗糙度、轮廓和许多其他表面参数的测定。
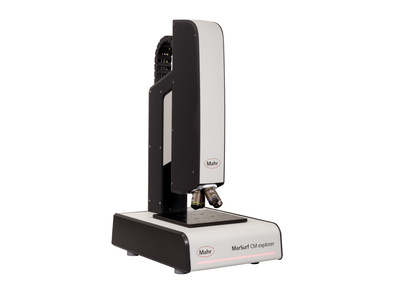
表面计量方法,工业和研究用
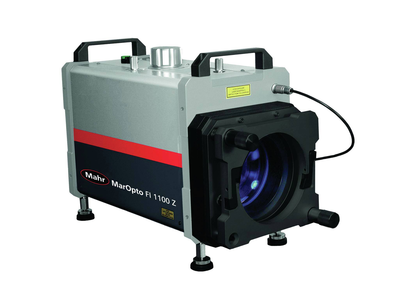
无论是白光还是激光干涉仪,您都会找到适合您应用的解决方案。
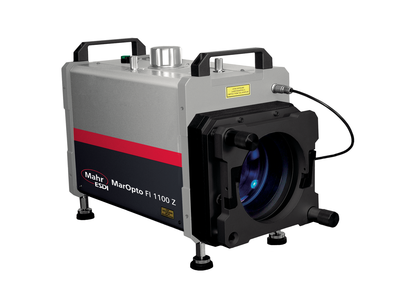
强大的 MarOpto Fizeau 干涉仪可以提供平面和球面的非接触测量。
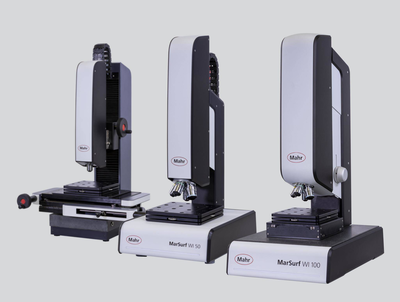
纳米计准确的最小粗糙度

表面拓扑结构和几何形状的光学分析

拥有成熟 Mahr马尔 质量的翻新系统
案例研究:测量池中的车削零件测试


在不同行业的许多装配中都要用到小型车削零件。这些高要求的工件是按照完全符合规格的千分之一毫米精度进行生产的。位于卡尔斯鲁厄附近布雷滕的 Klumpp 是世界领先的车削零件制造商之一,专门从事此类高精度车削零件的大规模生产。其产品的尺寸在 4 到 32 mm 之间。Klumpp 用不同的材料和高度复杂的功能制造它们。为了满足客户的需求,Klumpp 依靠现代化的生产技术和高质量的加工方法。
必要的重新定位
为此,该公司还决定对自身的质量管理进行检验。实现:以前的程序非常复杂,由于操作员的因素可靠性并非 100%。根据今天的标准,结果也无法记录。此外,控制必须在精密测量室内进行—远离生产线不说,还与耗时的物流相关。
对 Klumpp 来说,这些弱点是其在质量保证方面对自身重新定位的充足理由。作为事业部经理,负责计量技术的 Evelin Kobiljar 与 Mahr 一起制定了一个新理念:以持续、接近生产并可记录的方式监控生产质量。
解决方案:生产中的测量池
新解决方案的核心是一个加盖的空调测量池,它直接位于生产中。这样可以防止污染,并确保气候条件的一致性。机器操作员自己在这里进行测量。
Kobiljar 在测量池内建立了一个测试设备协调系统。它具有工艺可靠性,保持绝对测量稳定,并获得了精密测量室认可。使用的测量程序仍在精密测量室中创建,因为这是质量管理的责任所在。所有设备都从那里获取当前的测量程序,这是确保测量安全可靠的重要基础。
成功的四个步骤
根据新的测量概念,质量保证分四个步骤进行:
第 1 步:第一步是确定责任员工以及样本本身。后者通过读取二维码来识别。这一步骤对于记录非常重要—同时也带来了另一个优势:测量总是使用正确的最新测量程序进行。
第 2 步:然后,用四个 Mahr 数字千分表自动测量内部尺寸。测量结果通过电缆传输到轴测量系统,然后利用这些结果进行后续测试。


第 3 步:记录内部尺寸后,Klumpp 员工用全自动光学测量系统 MarShaft Scope 350 plus 检查工件的外部尺寸。操作员将工件夹入测量系统,然后开始测量。系统在短短 15 秒内就可以测量共计 40 个外轮廓特征,如直径、长度、半径和角度。测量序列全自动执行,不受操作员影响。


第 4 步:当所有测量完成后,所有内部和外部测量的测量数据被发送到质量管理系统,在那里对测量进行评估和记录。
测量概念的优势
新的测量解决方案为 Klumpp 及其质量保证工作人员带来了许多优势:
- 随着手持仪器数量的大幅减少,质量保证成本下降。
- 校准和仪器管理的成本和工作量下降。在几个月内就收回了对测量仪器和系统的投资。
- 测量更加高效和可靠—并且始终不受操作员的影响。
- 对于生产是否在生产公差范围会内有快速反馈,因此可以有效且可衡量的方式避免成本高昂的废品或投诉。
结论
总的来说,Klumpp 的整体制造质量保证现在更加高效和可靠。现在,由于新的测量概念已成功通过了考验,Klumpp 将从生产中大幅度剔除手动计量,取而代之的是,总共要建立 7 个标准化的测量池。该公司因此实现了目标:即在生产中可靠地确保精密车削件的生产质量。